CYCLE/TURN
automatically generates the g-code necessary to remove excess stock
during outside and inside rough turning. It requires a closed
profile path defined by standard APT part programming that defines the
start and end points of the path and the profile of the part being
turned. "Closed" means that the profile path begins and ends at
the same cutter location. A full example of the command's usage
is shown later on this page. The syntax of the command is:
CYCLE/TURN, index number, cutter diameter, radial depth of cut, axial feedrate, radial feedrate.
Index number defines the index number that encompasses the closed profile path. For example:
INDEX/1
APT command
APT command
.
.
.
INDEX/1,NOMORE
Cutter diameter
is (no surprise) the actual diameter of the cutter used in rough turning the
part. In usage the part programmer defines an oversized cutter
when defining the profile path so that material is left for a finishing
pass. For lathes the cutter diameter is the tool nose radius of
the cutter multiplied by 2. Example:
CUTTER/.084
$$ (.032 tool nose radius + .010)
* 2 will leave .010 on all surfaces for the finish pass
CYCLE/TURN,1,.064,.050,.010,.003 $$ .032 tool nose radius * 2 = the actual diameter
.
.
.
Radial depth of cut
specifies the X-axis depth of cut to take for each roughing pass.
For example, a value of .050 will take .100 off of the diameter
during each roughing pass.
Axial feedrate
specifies the feedrate generated for Z-axis only or combined X- and
Z-axis moves. The value specified is used literally so be
aware when using feedrates in units per revolution versus units per
minute. For example, specifying .010 causes F0.01 to be generated
and specifying 10.0 causes F10.0 to be generated.
Radial feedrate specifies the feedrate generated for X-axis only moves, i.e. plunge cuts in X+ or X-.
DO NOT transform the cutter locations when defining the profile path.
The CYCLE/TURN command requires the actual cutter center point
locations when calculating intersections. CYCLE/TURN will
automatically apply tool nose radius compensation (i.e. TRACUT) in the
generated g-code using the specified cutter diameter. For finish
passes it is
fine to use the standard TRACUT command to compensate for the tool nose
radius.
A
final pass to remove any left-over stock is done when all of the
roughing passes are completed. This final pass follows the
profile path defined by the part programmer.
Following is a
sample profile of a part to be turned. Note the start/end point
which both opens and closes the profile path. This also defines a
point at which the cutter will clear the rough stock dimensions for
both length and radius. The red arrows show the direction of the tool path.
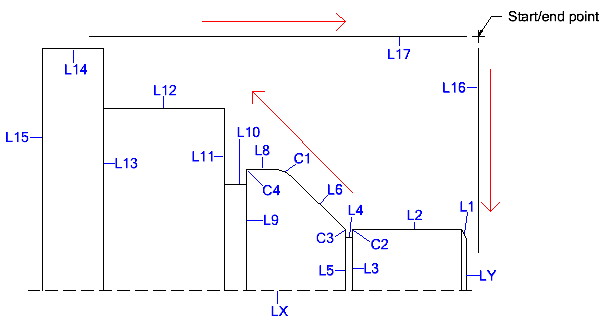
In
this image the closed profile path defined by the APT source is shown in red.
In the APT source (shown later on this page) the path is defined by all of the
statements between the INDEX/1 and INDEX/1,NOMORE statements.
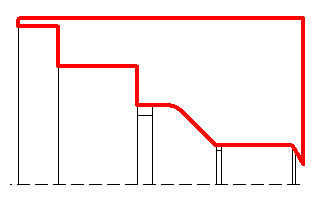
Following
is a screen shot of the final tool paths in the NC plotter,
plotted directly from the generated NC tape file. All of the horizontal
turning cuts plotted in dark blue were automatically generated by the
postprocessor using the CYCLE/TURN command. More sample plots are shown below.
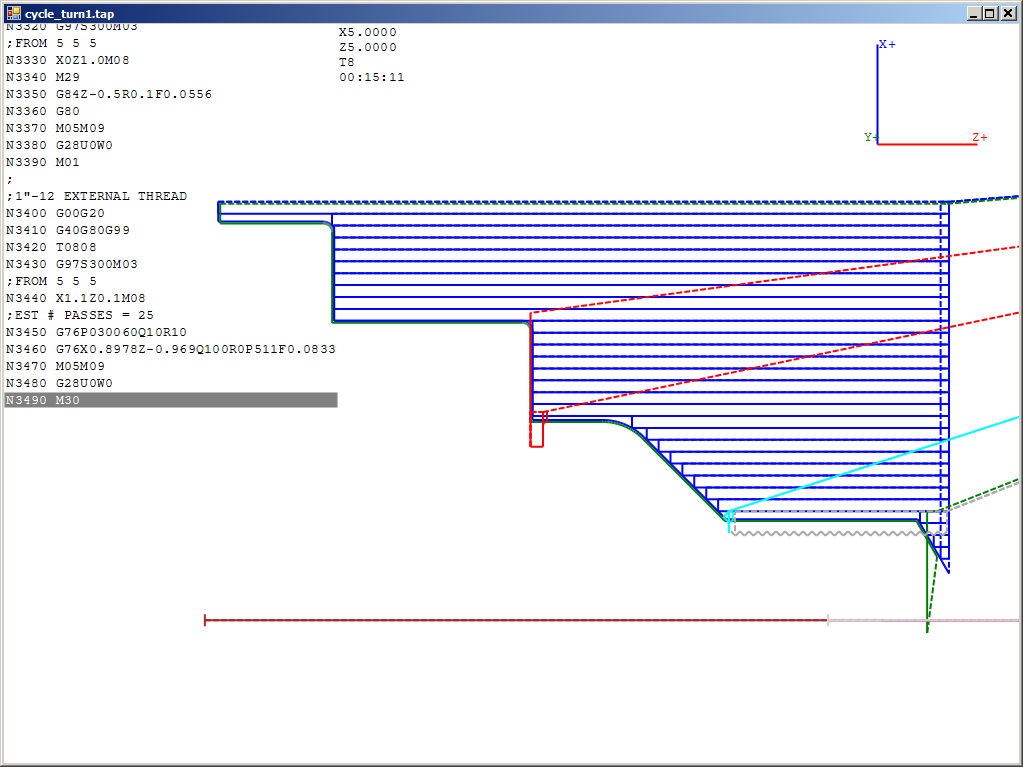
Following is the APT source for the entire part.
MACHIN/ACORNL
PARTNO CYCLE/TURN 1
SEQNO/1000,INCR,10,1
PRINT/ON $$ This controls the printing of canon data after each geometric definition
CLPRNT
$$ This controls the printing of postprocessor data. Options are "ON",
"OFF", AND "OPTION".
SYN/ AA,ATANGL, CA,CANON, CE,CENTER, CI,CIRCLE, CY,CYLNDR, DC,DNTCUT, $
FR,FEDRAT, GB,GOBACK, GD,GODLTA, GF,GOFWD, GL,GOLFT, GR,GORGT, $
GT,GOTO, IP,INDIRP, IV,INDIRV, IT,INTOF, LF,LEFT, LI,LINE, $
MX,MATRIX, OB,OBTAIN, PA,PARLEL, PD,PENDWN, PU,PENUP, PP,PERPTO, $
PL,PLANE, PT,POINT, RA,RADIUS, RT,RIGHT, TT,TANTO, TH,THICK, $
TA,TLAXIS, TL,TLLFT, TN,TLON, TR,TLRGT, VE,VECTOR, XL,XLARGE, $
XS,XSMALL, YL,YLARGE, YS,YSMALL, ZL,ZLARGE, ZS,ZSMALL, RP,RAPID
HOME=PT/5,5,5
LX=LI/XAXIS
LY=LI/YAXIS
L1=LI/(PT/0,(.86/2)),AA,30,YAXIS
L2=LI/PA,LX,YL,(1.0/2)
L3=LI/PA,LY,XS,(1.0-.062)
L4=LI/PA,LX,YL,(.88/2)
L5=LI/PA,LY,XS,1.0
L6=LI/(PT/-1.0,(1.0/2)),AA,-45,XAXIS
L8=LI/PA,LX,YL,(2.0/2)
L9=LI/PA,LY,XS,(2.0-.188)
L10=LI/PA,LX,YL,(1.75/2)
L11=LI/PA,LY,XS,2.0
L12=LI/PA,LX,YL,(3.0/2)
L13=LI/PA,LY,XS,3.0
L14=LI/PA,LX,YL,(4.0/2)
L15=LI/PA,LY,XS,3.5
L16=LI/PA,LY,XL,.1
L17=LI/PA,L14,YL,.1
C1=CI/YS,L6,YS,L8,RA,.25
C2=CI/YS,L2,XL,L3,RA,.010
C3=CI/YS,L6,XS,L5,RA,.010
C4=CI/YS,L8,XL,L9,RA,.010
PL0=PL/0,0,1,0
$$************* ROUGH TURN, .032 RADIUS TOOL **************************
PPRINT
PPRINT ROUGH TURN, .032 RADIUS TOOL
$$ This macro defines the bulk of the profile path
$$ along with the additional statements enclosed by the
$$ INDEX statements. This macro is also called when
$$ the finish passes are defined. Using a macro is not
$$ required. It just simplifies part programming and
$$ saves a bit of typing.
RTURN=MACRO
GL/L2
GR/L6
GF/C1
GF/L8
GR/L11
GF/(CI/XS,L11,YS,L12,RA,.010)
GF/L12
GR/L13
GF/(CI/XS,L13,YS,L14,RA,.010)
GF/L14,PAST,L15
GO/PAST,L17
RP,GO/PAST,L16
TERMAC
RESET
TURRET/1,1
ORIGIN/54
SPINDL/500,SFM,CLW,MAXRPM,10000
COOLNT/ON
FROM/HOME
CUTTER/.084 $$ declare oversized cutter diameter for rough turning
FEDRAT/.008 $$ declare a default feedrate just to be safe
$$ In the following CYCLE/TURN command:
$$ 1 = The index number that defines the closed profile path
$$
.064 = The actual cutter diameter. Note that an oversized cutter
is declared above which will leave .010 on all surfaces for clean
up.
$$ .060 = The radial depth of cut.
$$ .008 = The axial feedrate.
$$ .003 = The radial (i.e. plunge) feedrate.
$$ Note that the tool path for the CYCLE/TURN is not (and must not) be transformed in any manner.
$$ The finish operation coded later uses TRACUT per standard lathe programming.
CYCLE/TURN,1,.064,.060,.008,.003
INDEX/1
RP,GO/L16,PL0,L17 $$ this is the start/end point and matches the ending location in the macro
RP,GO/L16,PL0,L1
TR,GR/L1
CALL/RTURN
INDEX/1,NOMORE
COOLNT/OFF
SPINDL/OFF
RP,GOHOME
OPSTOP
$$************* FINISH FACE AND TURN, .032 RADIUS TOOL ****************
PPRINT
PPRINT FINISH FACE AND TURN, .032 RADIUS TOOL
RESET
TURRET/2,2
ORIGIN/54
SPINDL/500,SFM,CLW,MAXRPM,10000
COOLNT/ON
FROM/HOME
CUTTER/.064
FEDRAT/.008
TRACUT/(M1=MATRIX/TRANSL,-.032,-.032,0) $$ TRACUT by the actual tool nose radius.
$$ FINISH FACE
CUTCOM/LEFT
RP,GO/(LI/PA,LY,XL,.05),PL0,(LI/PA,L2,YL,.05)
GO/LY
GO/PAST,LX
CUTCOM/OFF
GO/PAST,(LI/PA,LY,XL,.05)
$$ FINISH TURNING
CUTCOM/RIGHT
RP,GO/(LI/PA,LY,XL,.05),PL0,PAST,L1
TR,GL/L1
CALL/RTURN
CUTCOM/OFF
TRACUT/NOMORE
COOLNT/OFF
SPINDL/OFF
RP,GOHOME
OPSTOP
$$ *************** 1/16 (.062) GROOVING, .010 RADIUS ******************
PPRINT
PPRINT 1/16 (.062) GROOVING, .010 RADIUS
RESET
TURRET/3,3
ORIGIN/55
SPINDL/500,SFM,CLW,MAXRPM,3000
COOLNT/ON
FROM/HOME
CUTTER/.020
TRACUT/(M2=MATRIX/TRANSL,-.010,-.010,0)
RP,GO/L5,ON,PL0,(LI/PA,L2,YL,.050)
FEDRAT/.002
GO/L4
RP,GO/PAST,(LI/PA,L2,YL,.050)
GO/L6
TL,GL/L6
GF/C3,TT,L5
RP,GO/PAST,(LI/PA,L2,YL,.050)
TRACUT/NOMORE
TRACUT/(M3=MATRIX/TRANSL,-.052,-.01,0) $$ X VALUE = -(TOOL WIDTH - TOOL RADIUS)
RP,GO/ON,(LI/(PT/CE,C2),PP,LX)
GO/C2
TR,GR/C2,TT,L3
RP,GO/PAST,(LI/PA,L2,YL,.050)
TRACUT/NOMORE
COOLNT/OFF
SPINDL/OFF
RP,GOHOME
OPSTOP
$$ *************** 1/8 (.125) GROOVING, .010 RADIUS *******************
PPRINT
PPRINT 1/8 (.125) GROOVING, .010 RADIUS
RESET
TURRET/4,4
ORIGIN/55
SPINDL/500,SFM,CLW,MAXRPM,3000
COOLNT/ON
FROM/HOME
CUTTER/.020
TRACUT/M2
RP,GO/L11,ON,PL0,(LI/PA,L12,YL,.050)
FEDRAT/.002
GO/L10
RP,GO/PAST,(LI/PA,L8,YL,.050)
TRACUT/(M4=MATRIX/TRANSL,-.115,-.01,0) $$ X VALUE = -(TOOL WIDTH - TOOL RADIUS)
RP,GO/L9
GO/L10
TRACUT/NOMORE
TRACUT/M2
GO/L11
RP,GO/PAST,(LI/PA,L8,YL,.050)
TRACUT/NOMORE
TRACUT/M4
RP,GO/ON,(LI/(PT/CE,C4),PP,LX)
GO/C4
TR,GR/C4,TT,L9
RP,GO/PAST,(LI/PA,L8,YL,.050)
TRACUT/NOMORE
COOLNT/OFF
SPINDL/OFF
RP,GOHOME
OPSTOP
$$********** 90 DEGREE SPOT DRILL TO .460 DIAMETER ********************
PPRINT
PPRINT 90 DEGREE SPOT DRILL TO .460 DIAMETER
RESET
TURRET/5,5
REVS=(500*3.82)/.5 $$ RPM = (SFM * 3.82) / dia
SPINDL/REVS,RPM,CLW
COOLNT/ON
FROM/HOME
RP,GOTO/1,0,0
CYCLE/DRILL,(-.460/2),.1,.002
CYCLE/OFF
COOLNT/OFF
SPINDL/OFF
RP,GOHOME
OPSTOP
$$******************* 7/16 (.438) DRILL THRU **************************
PPRINT
PPRINT 7/16 (.438) DRILL THRU
RESET
TURRET/6,6
REVS=(500*3.82)/.438 $$ RPM = (SFM * 3.82) / dia
SPINDL/REVS,RPM,CLW
COOLNT/ON
FROM/HOME
RP,GOTO/1,0,0
DPTH=3.5+(TANF(31)*(.438/2))+.01
CYCLE/DEEP,-DPTH,.1,.004,(.438/2)
CYCLE/OFF
COOLNT/OFF
SPINDL/OFF
RP,GOHOME
OPSTOP
$$*********************** 1/4-18 NPT TAP ******************************
PPRINT
PPRINT 1/4-18 NPT TAP, DEPTH IS ONLY A GUESS
RESET
TURRET/7,7
SPINDL/300,RPM,CLW
COOLNT/ON
FROM/HOME
RP,GOTO/1,0,0
CYCLE/TAP,RIGHT,-.5,.1,(1/18) $$ Depth is only a guess.
CYCLE/OFF
COOLNT/OFF
SPINDL/OFF
RP,GOHOME
OPSTOP
$$ *************** 1"-12 EXTERNAL THREAD ******************************
PPRINT
PPRINT 1"-12 EXTERNAL THREAD
RESET
TURRET/8,8
SPINDL/300,RPM,CLW
COOLNT/ON
FROM/HOME
RP,GOTO/.1,.55,0
$$
pitch, major diameter, z, depth of first cut, min
depth of cut, depth of last pass, pull out, taper, infeed angle, spring
passes
THREAD/(1/12),(1-2*(1/12)*.61343),(-1.0+.031),.01,.001,.001,0,0,60,3
COOLNT/OFF
SPINDL/OFF
RP,GOHOME
REWIND
FINI
Here is another plot showing OD roughing and finishing with an undercut:
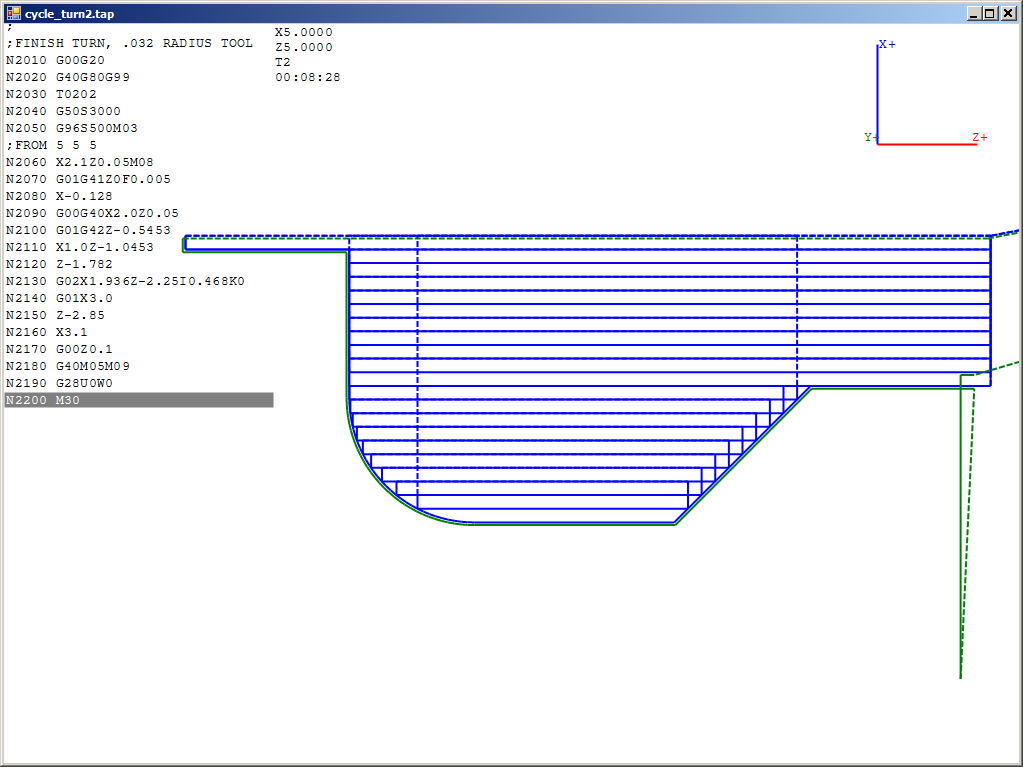
Here is an example path and plot showing roughing out a bore:
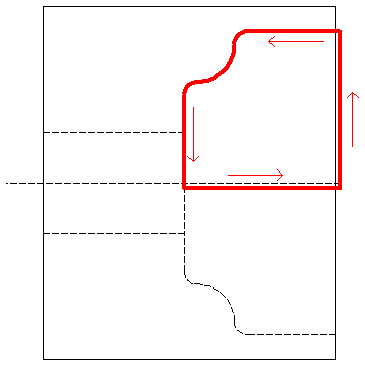
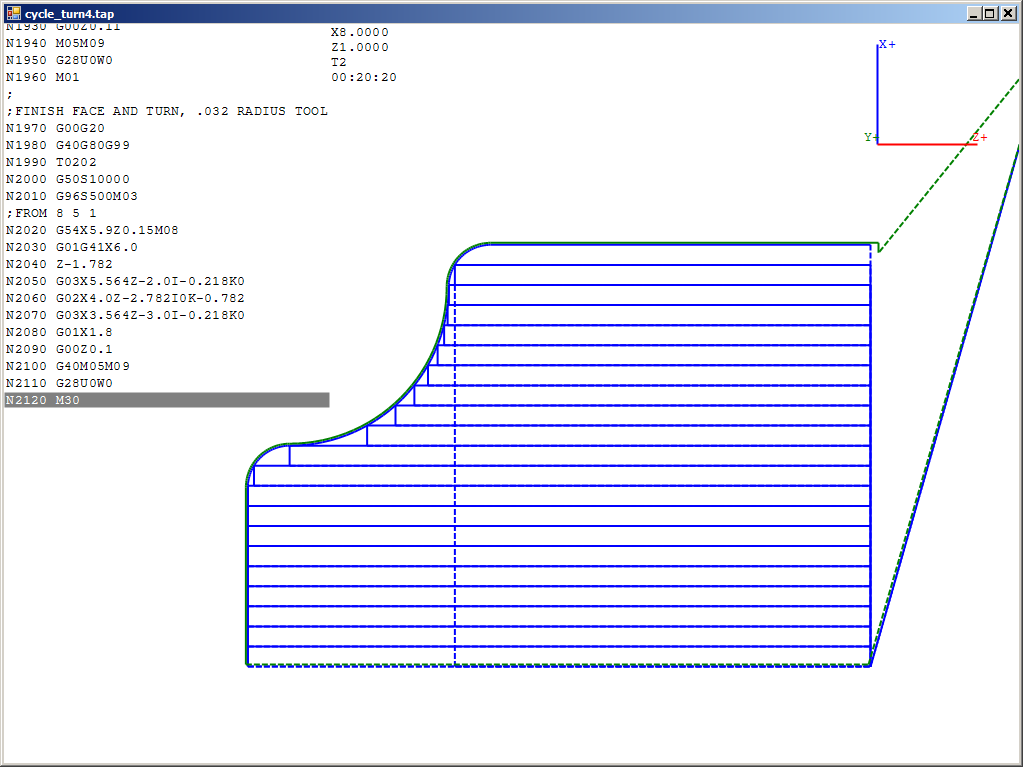
And here is a chess pawn being roughed and finished turned and parted off:
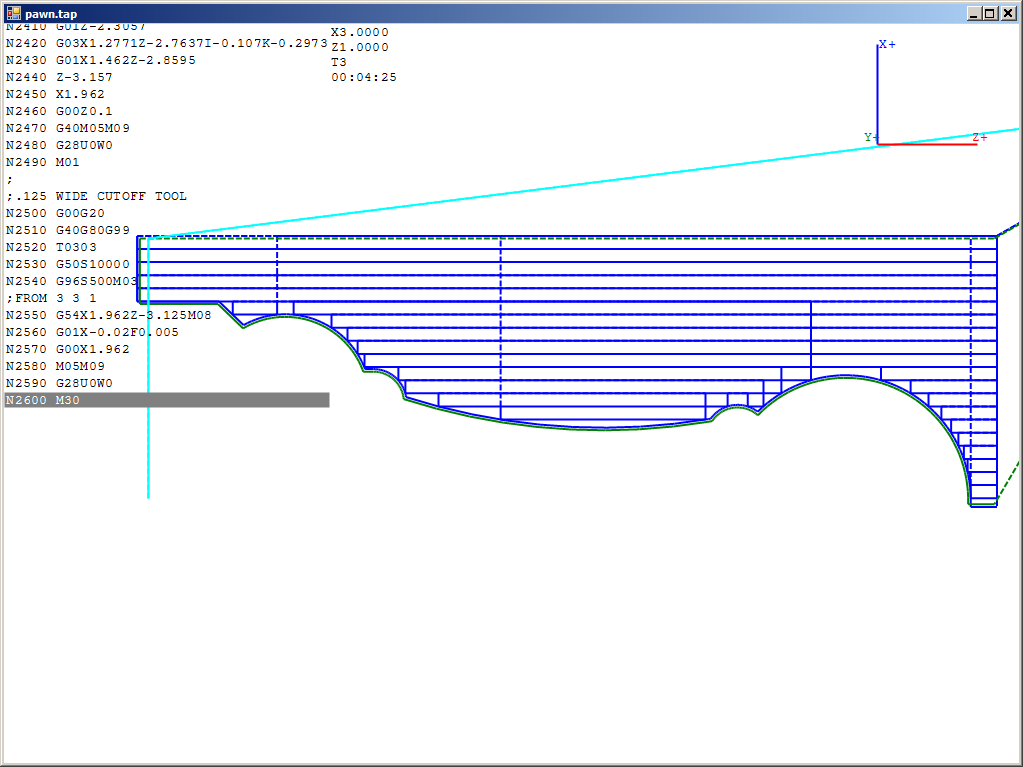